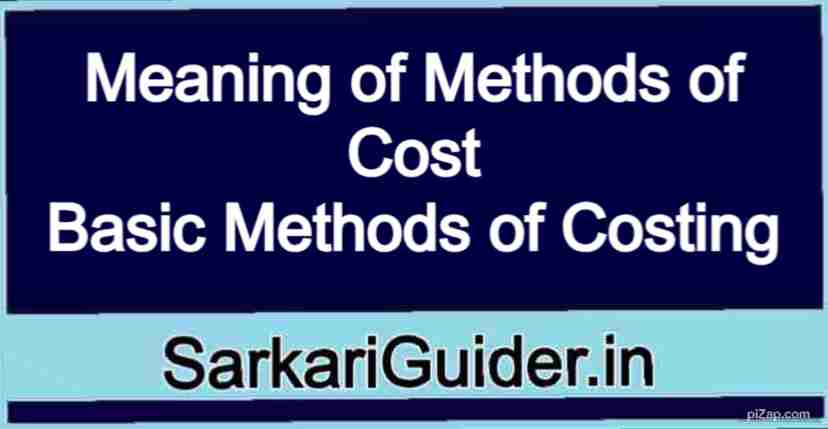
Meaning of Methods of Cost – The term methods of costing can be used to refer to the different processes or procedures employed for the determination and presentation of costs. There are different methods of costing for different industries depending on their nature of work.
For example, the chemical industry follows a continuous production process where raw material is processed at different stages. There are other industries which undertake jobs of different kinds.
For example, a motor workshop accepts different jobs. In industries like transport. banks or insurance, the whole activity centers ty around certain service operations. Similarly, many other industries may undertake production of only one product.
Since the very nature of production processes and the Meaning of Methods of Cost of word differ from industry to industry, it becomes imperative to use different methods of costing.
However, there are two basic methods of costing, which are:
(i) Job costing
(ii) Process costing
All other methods of costing are either a variation, improvement, extension or combination of these two basic methods.
1. What is Single costing, unit costing or output costing
Single costing is adopted in concerns where production is continuous and where only one product or a few types of similar products, which vary only in size, shape and quality and whose output can be measured by a common unit, are product.
Under this method, the cost per unit of output such as per ton, per barrel, per kilogram, per meter, per quintal, per bag, etc. is ascertained.
The industries where this method of costing is applied are mines quarries, collieries, breweries, all drilling companies, steel works, cement factories, paper mills, flour mills, exile mills, etc.
2. What is Definition Job Costing
Job costing is adopted in concerns where the work done is analyzed into different jobs, cache job being considered as separate unit of cost. Under this method the cost of cache job and the profit or loss made on each job under-taken is found out separately.
A separate account is opened for each job to which all expenses incurred on that job, from the date of commencement till the date of completion, are debited. This will enable the concern to know the cost of each job.
By comparing the cost of each job against the price charged for each job, the profit or loss made on each job is ascertained.
The concerns where this method of costing is applied are printing process, motors workshop, watch repair works, etc.
3. What is Contract Costing or Terminal Costing
Contract costing is adopted where a job is very big and takes a long time to complete. Under this method of costing the cost of each contract is ascertained separately.
It is suitable for those firms which are engaged in the construction of bridges, roads, building. factories etc. on a contract basis.
4. What is meaning of Batch Costing
Where small components of the same kind are required to be manufactured in large quantities, the method of costing used is called batch costing.
Under this Meaning of Methods of Cost a batch of similar products is treated as a job and the costs are accumulated in respect of a batch.
In a bicycle producing factory, if rims are produced in batches of 5,000 each, cost will be determined in relation to a batch of 5.000 rims.
5. What is Process Costing
In industries where a continuous process of production is carried and the product is homogeneous, the method of ascertaining the cost of the product is called Process Costing.
As distinct from job these industries costing, in the cost of cache process is determined for a given period of time. Product loss their individual as they are manufactured in a continuous flow.
This method of costing is extensively used in steel, sugar, textiles, chemicals, soap, Vanaspati. paper and pain manufacturing organizations.
6. What is Meaning of Operation Costing
Operation costing is a more detailed application of Process Costing Under this method, the cost of each distinct operation of a process, instead of the cost of the process as a whole, is ascertained. This method provide minute analysis of costs and ensures greater accuracy and better control of costs.
It is adopted in concerns where the manufacturing process consists of a number of distinct operations. Toy making units engineering, industries timber works, leather tanneries etc. adopt this method.
7.Definition Operating Costing
The method of costing, which is used in service rendering undertakings is called operating costing. For example, transport water supply, electric undertakings, telephone services. hospitals, nursing homes, etc. use this method of costing.
A special feature of operating costing is that the unit of cost is generally a compound unit. For example the units of cost in electricity supply is kilowatt hour.
8. What is Meaning of Uniform Costing
When various undertaking, under the same or under different managements in the same industry, use the same principles or practices of costing, they are said to be using the method of uniform costing.
In such a situation all costing information is dealt within a similar manner. The use of uniform costing facilitates inter-firm comparison.
9.Definition Departmental Costing
This system is applicable where the cost of a department or a cost center is required to be ascertained. This is similar to operating costing.
This system is resorted to where the factory is divided into distinct department and it is desired to ascertain the cost of production of each department rather than the cost of each article produced. This method is good for a comparative study of the identical costs of different departments.
Under this method, the cost of operating each department is ascertained by allocating the total expenses incurred by a concern to various department, and the cost per unit of product produced in cache department is ascertained by dividing the total cost of the department by the number of units produced in that department.
This method is adopted by concerns producing hosiery goods. factories producing cosmetics, footwear manufacturing concerns, etc.
10. Meaning of Cost Plus Methods
Where a businessman feels hesitant to quote for a work which is absolutely new to him and new to other persons or contractors and he is unable to estimate the cost of the works offered to him for execution.
It is decided with the contractor that he would be paid the total cost of work whatever it be, plus his profit at a certain percent on the total cost Such type of work is called cost plus Methods.
इसे भी पढ़े…
- Definition of Primary Distribution of Overheads
- What is Re-Apportionment of Service Departments Overheads
- Process of Classification of Overheads | Basis of Overhead Classification
- What is Overheads | Bases For Allocation of Expenses to Departments
- What is Meaning of Incentive Wage Method | Methods of Wage Payment
- Meaning of Collection Allocation | Apportionment of Overhead Expenses
- What is Primary Distribution of Overheads
- What is Meaning of Overhead | Classification of Overhead
- Process of Classification of Overheads | Basis of Overhead Classification
- Advantages of Fixed and Variable Overheads | Difference Between Fixed & Variable Overheads
- What is Absorption of Selling and Distribution Overheads
- What is Money, Definition, Functions and various kinds of Money
- What is Apportionment of Overheads, Principles, Difference