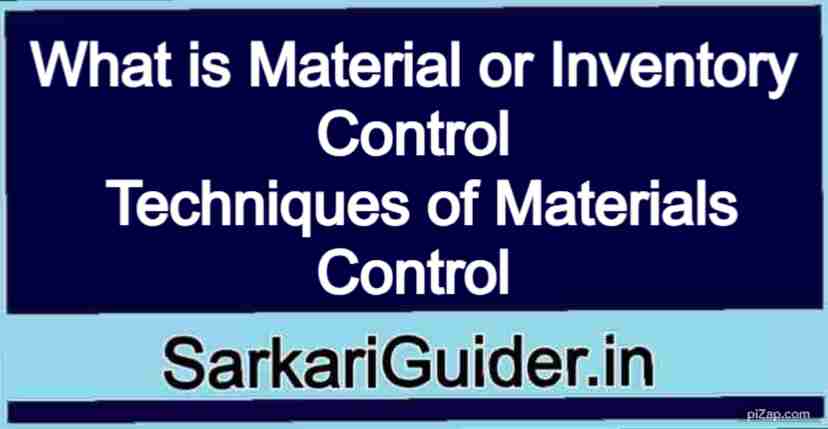
Material or Inventory Control
No cost accounting system can become effective without proper and efficient Material or inventory control. This is so because quite often material is the largest single element of cost and as such on efficient system of material control leads to a significant economy in the total cost.
Material is as much as cash itself and any theft, waste and excessive use of materials are immediate and direct financial losses.
Material or inventory control may be defined as “Systematic control and regulation of purchase, storage and usage of materials in such way so as to maintain and even flow of production and at the same time avoiding excessive investment in inventories Efficient material control cuts out losses and wastes of material that otherwise pass unnoticed.”
Thus and efficient system of material control should be comprehensive enough to cover purchase system, storage system, issue to production and determining stock levels for each item of material.
Objective of Material of Inventory Control
The main objective of material control are discussed below:
1. No under-stocking
Under-stocking may leads to shortage of materials. Shortage of material may arise at a time when they are urgently needed and production may then be help up.
The delay or shortage in production due to non availability of material is very cost and results in loss of profit. Thus material control system helps in maintaining no under-stocking.
2. No Over-stocking
Investment in materials must be kept as low as possible considering the production requirements and the financial resources of the business.
Over-stocking of materials locks up capital and causes high storage costs thereby resulting in adverse effect on profit. This may also result in loss due to obsolescence.
3. Economy in purchasing
This purchasing of materials in highly specialized function. By purchasing materials at the most favorable prices the purchaser is able to make a valuable contribution to the reduction in cost.
4. Material of Good Quality
While purchasing materials, due consideration should be given to the quality of material. It is no use purchasing materials of inferior quality or very superior quality.
For each type of product, there is a product, there is a particular type quality of material which is needed and that quality alone should be purchased.
5. Minimum Wastage
In order to minimize the loss on material proper storage conditions must be provided to different types of material. Losses of materials occur due to determination, obsolescence, pilferage and theft. evaporation, etc.
All round efforts should be made to keep these losses at the minimum.
6. Information about Material
Not only that materials should be available when required, but there should also be a system to give complete and up-to-date accounting information about the availability of materials.
Sometimes information about availability of materials may cause new purchases to be made of materials already in stock.
The fulfilment of the above objectives of material control will require keeping of proper material records. The lists of all materials and store required by a firm for the production should be drawn up together with at least weekly consumption figures.
Also the lead time for each item has to be determined. which will enable a firm so ascertain the minimum quantity required of each item in stock.
It is also necessary to fix the maximum quantity of stock at any point of time to ensure that capital is not licked up unnecessarily and the risk of obsolescence is minimized. Use of ABC analysis and EOQ formula can be of great help in this regard.
Essential Requirement of Inventory Control
The following are the essential requirements of a successful material control system:
1. There should be proper coordination in all concerned departments, production department, purchasing department, receiving department, inspection department, storage and accounting department, etc.
2. There should be central purchasing department under the control of a competent and expert purchase manager.
3. There should be proper classification and codification of materials.
4. Perpetual inventory system should be operated so that up-to-date information is available about the quantity of material in stock.
5. Adequate records should be introduced to control materials during production and the quantities manufactured for stock.
6. Preparation of budgets concerning materials, supplies and equipment to ensure economy in purchasing and use of materials.
7. Materials requirements should be properly planned.
8. The storage of all materials should be will planned subject to adequate safeguards and supervision.
9. The various stock levels like, minimum stock level, maximum stock level, etc. should be fixed for each item of material.
10. An efficient system of internal audit and internal check should be operated so that all transactions involving materials are checked by reliable and independent persons.
11. There should be regular reporting to management regarding purchase, issues and stock of materials. Special reports should be prepared for obsolete item, spoilage, returns to suppliers, etc.
Techniques of Materials Control
Following are the main techniques of materials control:
(a) ABC Analysis
The concept of ABC Analysis was coined by Pareto, an Indian philosopher in the nineteenth century. It is a value based system of material control.
In this technique materials are analyzed according to their value so that costly and more valuable materials are given greater attention and care.
All items of materials are classified according to their value – high, medium and low values, which are known as A, B and C item respectively. ABC technique is some time called as “Always better control” method.
‘A’ Items – These are high value item which may consist of only a small percentage of the total item handled. On account of their high cost, these materials should be under the tightest control and the responsibility of the experienced personnel.
‘B’ Items – These are medium value materials which should be under the normal control procedures.
‘C’ Items – These are low value materials which may represent a very large number of items. Theses materials should be under the simple and economic methods of control.
The point of classifying stock into A, B and C categories is to ensure that material management focuses on ‘A’ item where tightest control should be installed.
B item be given less attention and C item least attention. The ABC technique is a selective control which aims at concentrating efforts on those materials where attention is needed most.
This is so because it is unwise to give equal attention to all items in stock. The items are listed and ranked in the order of their descending importance showing quantity and value of each item.
Advantages of ABC Analysis
Following are the main advantages of ABC Analysis:
I. A strict control can be exercised on those items which represent large amount of capital invested.
2. Investment in inventory is regulated and funds can be utilized in
the best possible way.
3. Storage cost also will be less as only the required quantity materials alone are purchased.
4. Quick purchase of materials can be ensured by concentrating on fewer items that are required at one time.
5. It is based on the principle of control by exception which gives results especially when resources and staff are less.
6. It helps in maintaining enough safety stock for ‘C’ category items.
(b) Determination of Stock Levels
In order guard against under stocking to most and over stocking large companies adopt a scientific approach of fixing stock levels. These levels are-
(i) Maximum level
(ii) Minimum level
(iii) Re-order/ordering level
(iv) Danger level. etc.
These levels are not permanent and must be changed to suit changing circumstances. Thus. changes will take place if consumption of materials is increased or decreased or if in the light of a review of capital available, it is decided that the overall inventory must be increased or decreased.
The Modern Inventory Management makes use of research and statistical techniques in fixing stack-levels. However, given below is the description of various levels along with formula that are commonly used in their computations.
Factors Affecting Stock Levels: Some of the factors which influence the stock levels are-
1. Anticipated rate of consumption,
2. Amount of capital available
3. Availability of storage space
4. Cost of storing
5. Procurement costs
6. Reliability of suppliers.
7. Minimum order quantities imposed by suppliers 8. Risk of loss due to
(a) obsolescence
(b) Deterioration
(c) Evaporation
(d) Fall in market prices, etc.
Maximum Stock Level
This is that level above which stocks should not normally be allowed to rise. The maximum level may however, be exceeded in certain cases, e.g., when usually favorable purchasing condition arise. It is computed by the following formula:
Maximum Stock Level = Re-order level + Re-order Quantity (Mini. Consumption x Mini Re-order Period)
The following factors are taken into account in setting this level:
1. Rate of consumption of material
2. Risk of obsolescence and deterioration 3. Storage space available
4. Cost of storage and insurance
5. Availability of funds needed
6. Seasonal considerations, e.g. bulk purchases during seasons at low prices.
7. Reorder Quantity
8. Restrictions imposed by Government or local authority in respect of certain materials in which there are inherent risk of fire, explosion, etc.
The idea of setting maximum stock level is to ensure that capital in not unnecessarily blocked in stores and also to avoid loss due to obsolescence and deterioration.
Minimum Stock Level
It is that level which stock not normally be allowed to fall. This is essentially a safety stock and is not normally touched. In case of stock falling below this level, there is a risk of stoppage in production and thus top priority should be given to the acquisition of fresh supplies.
Minimum Stock Level = Reorder level – (Normal Consumption> Normal reorder period)
In fixing the level, the following factors are considered:
1. Rate of consumption.
2. The time required to acquire fresh supplies under top priority conditions so that stoppage in production can be avoided.
Re-order Level or Ordering Level
This is that level of material at which purchase requisition is initiated for fresh supplies. This level is fixed somewhere above minimum level.
This is fixed in such a way that by re-ordering when materials fall to this levels, then in the normal course of events, new supplies will be received just before the minimum level is reached. It is calculated with the help of following formula:
Re-order level = (Max. Consumption x Max. Re-order Period)
In fixing this level the following factors are taken into consideration
1. Rate of consumption of the material.
2. Minimum level.
3. Delivery time.
4. Variation in delivery time.
Danger Level
This is a level at which normal issues of materials are stopped and materials are issued for important jobs only. This level is generally fixed somewhat below the minimum level.
When stock reaches danger level, urgent action is needed for the replenishment of stock so that stoppage in production can be avoided. Purchasing materials on an urgent basis results in higher purchasing cost.
It is calculated with the help of following formula:
Danger Level = (Normal Consumption x Maximum re-order period under emergency condition)
Average Stock Level –
It is calculated with the help of following formula:
Average Stock Level =1/2(Mini. Stock level + Max. Stock level)
इसे भी पढ़े…
- Definition of Primary Distribution of Overheads
- What is Re-Apportionment of Service Departments Overheads
- Process of Classification of Overheads | Basis of Overhead Classification
- What is Overheads | Bases For Allocation of Expenses to Departments
- What is Meaning of Incentive Wage Method | Methods of Wage Payment
- Meaning of Collection Allocation | Apportionment of Overhead Expenses
- What is Primary Distribution of Overheads
- What is Meaning of Overhead | Classification of Overhead
- Process of Classification of Overheads | Basis of Overhead Classification
- Advantages of Fixed and Variable Overheads | Difference Between Fixed & Variable Overheads
- What is Absorption of Selling and Distribution Overheads
- What is Money, Definition, Functions and various kinds of Money
- What is Apportionment of Overheads, Principles, Difference